One of the core services we offer at Flowcav is one-dimensional modelling. one-dimensional simulation is an approach widely used accross a range of sciences including biology, physics, finance and many more. It provides a rapid yet powerful way of solving all types of engineering systems including multi- domain and multi-physics (Hydraulics, Thermal, Electromagnetic and so forth).
What is one-dimensional Simulation?, How does it work?, should I choose one-dimensional simulation or CFD for my problem?, What can you analyse using 1D simulation?. Find answers to all your pressing questions below.
What is one-dimensional Simulation?
Perhaps the best way to introduce one-dimensional simulation is by way of an example. Consider a chemical plant which has a cooling circuit consisting of electromechanically actuated valves, pipelines, pumps, thermally controlled switches and a control system. one-dimensional simulation allows for representative mathemathical models to be introduced for each component, providing for complete analysis of the system including transient effects. Typical outputs derived from such a simulation would include electrical current, fluid mass flowrate, dyanamic valve positioning, temperatures and hydraulic pressures.
The above is just a singular example of one-dimensional modelling. As will be detailed in later questions, one-dimensional simulation can be applied to a vast range of industrial products and processes.
How Does one-dimensional Modelling Work?
System simulation using one-dimensional analysis depends on the representation of numerous components in the form of mathematical models on a system map. The physical phenomena of each component is represented as a "macroscopic behaviour". Considering again the example of the chemical plant cooling circuit introduced in the previous question, in this case the thermostatically controlled switch could be represented by a mathemathical step function. This would act as a source of electric current above a certain threshold temperature. For more complex cmponents, predefined mathemathical representation templates can be selected from a range of predefined libraries, or alternatively, analytical or tabular based user defined representations can be created and used.
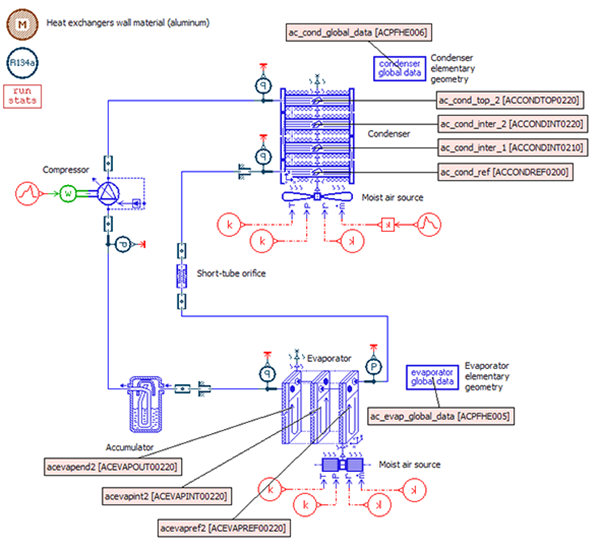
Above: Air Coonditioning System loop model with start/stop functionality.
By combining and customising library components, Flowcav can quickly create an easy to understand working sketch of the system model. Often, Flowcav engineers start from greatly simplified representations in the early development stages and gradually add more detail as design information becomes available.
CFD or one-dimensional Modelling?
one-dimensional analysis is a simple but not simplistic approach. It's primary use is for the analysis of systems rather than detailed analysis of singular components. In contrast, whilst the scope of CFD has continuously increased in recent years, with growing ability to model ever greater subsections, often modelling full systems can be prohibatively costly in terms of resources. Moreover, it can be the case that engineers are more concerned with the global output metrics rather than the detail level provided by CFD.
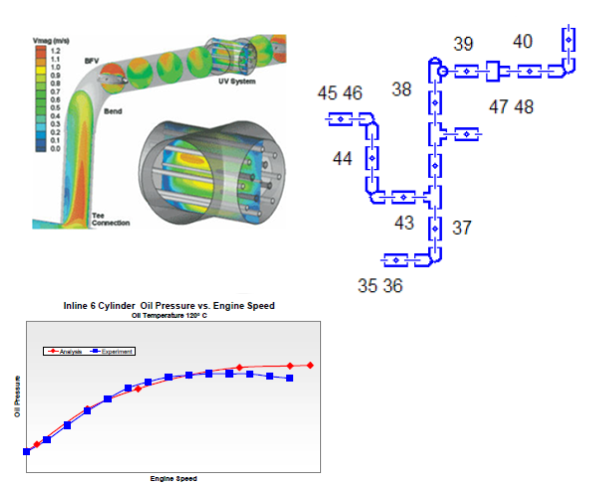
Above: CFD 3D Solution (Top Left) and one-dimensional Representation (Top Right), Comparison of 1D analysis and CFD results below.
In summary, one-dimensional analysis should be considered when:
- Rapid analysis is required
- System Analysis rather than component level
- Macroscale Information Required
one-dimensional Analysis is a proven and widely validated approach allowing critical design and development challenges to be overcome. It ensures products are delivered right first time. It brings about superior products that truely excite.
What can be Analysed / Application Areas?
At Flowcav, we have access to more than 38 customised libraries filled with over 5000+ dedicated models, covering a multitude of physical domains and engineering applications. As such, the possibilities for analysis are virtually endless. Our core libraries include:
- Fluid: Hydraulic, Hydraulic Component Design, Hydraulic Resistance, Filling, Pneumatic, Pneumatic Component Design, Gas Mixture, Moist Air
- Control: Signal, Control & Observers
- Electromechanical: Electrical Basics, Electromechanical, Electric Motors & Drives
- Internal Combustion Engine: IFP-Drive, IFP-Engine, IFP-Exhaust, IFP-Combustion 3D
- Mechanical: Mechanical, Planar Mechanical, Powertrain, Vehicle Dynamics
- Thermal: Thermal, Thermal-Hydraulic, Thermal-Hydraulic Component Design, Thermal-Pneumatic, Two-Phase Flow, Air Conditioning, Cooling System, Heat Exchanger Assembly Tools
At Flowcav, our range of experience in one-dimensional modelling has covered everything from high end multi-physics fuel injection technology to analysis of consumer heating products.
Typical objectives of one-dimensional simulation projects at Flowcav can include:
- System Design: Establish best performance while ensuring operating safety
- Component Design: Designing the component which fits the functional requirements of the system
- System Integration: Simulate the impact of the real component on the system
- Validate Control Strategies
- Run "What if.." scenarios offline
Why choose Flowcav for 1D Analysis?
When undertaking dimensional simulation, combining engineering science expertise with hands on real-world industrial knowledge is key to success. At Flowcav, we are confident that our engineers are the best in the business - in large part because of their ability to relate fluid analysis to hardware.
Our unique blend of skills and process know-how turns attribute-based engineering into a true competitive advantage for you. Here are several more good reasons to choose Flowcav for One-Dimensional Simulation:
- Our track record in one-dimensional modelling is unsurpassed. Our experience spans from concept and initial design optimization, detailed modelling and predictive studies to prototype refinement.
- Flowcav engineers are true partners who work with customers to solve their most critical design and development challenges. This knowledge transfer can make the difference between a successful product launch and costly recalls and repairs or even product failures.
- Access to the Best Analysis Tools: At Flowcav, we have tried and tested all the major one-dimensional software codes. Our present code has been extensively customised to our needs, which helps us to meet yours!. We have complete access to full range of libraries and features with no exceptions.
- Avoid layers of middle management: When dealing with Flowcav, customers have direct access to our engineer and are aware of exactly who is working on their problem, and how it is progressing.
- Doing buisness with us is easy: At Flowcav, as a small organisation, we believe in only taking on work which we can handle. We'll tell you straight whether we can assist you, what the likely cost and scope of work will be upfront. We respect that projects we work on can be commercially sensitive. To avoid any conflict of interest and provide reassurance for clients, we explicitly choose not to avoid working with competitors within the same industry.
Thinking of Pushing the Boundaries?
At Flowcav, as well as tackling the more routine analysis, we enjoy taking on the more demanding challenges and problems. This allows us to benchmark our performance against the very best, and ensure that we remain at the forefront of analysis
Two specific areas where we are pushing boundaries are as follows:
- CFD Analysis of Subsystems: We are now using full CFD analysis to model much more of systems than would previously have been possible
- Coupling of CFD with one-dimensional Analysis: Flowcav have access to customised software which allows us to couple one-dimensional analysis with CFD thereby giving a total hydraulic solution, with the optimum combination of speed and localised detail where required
By combining and customising library components, Flowcav can quickly create an easy to understand working sketch of the system model. Often, Flowcav engineers start from greatly simplified representations in the early development stages and gradually add more detail aas design information becomes available.
Contact Flowcav now and we will happy to answer any further questions you may have.